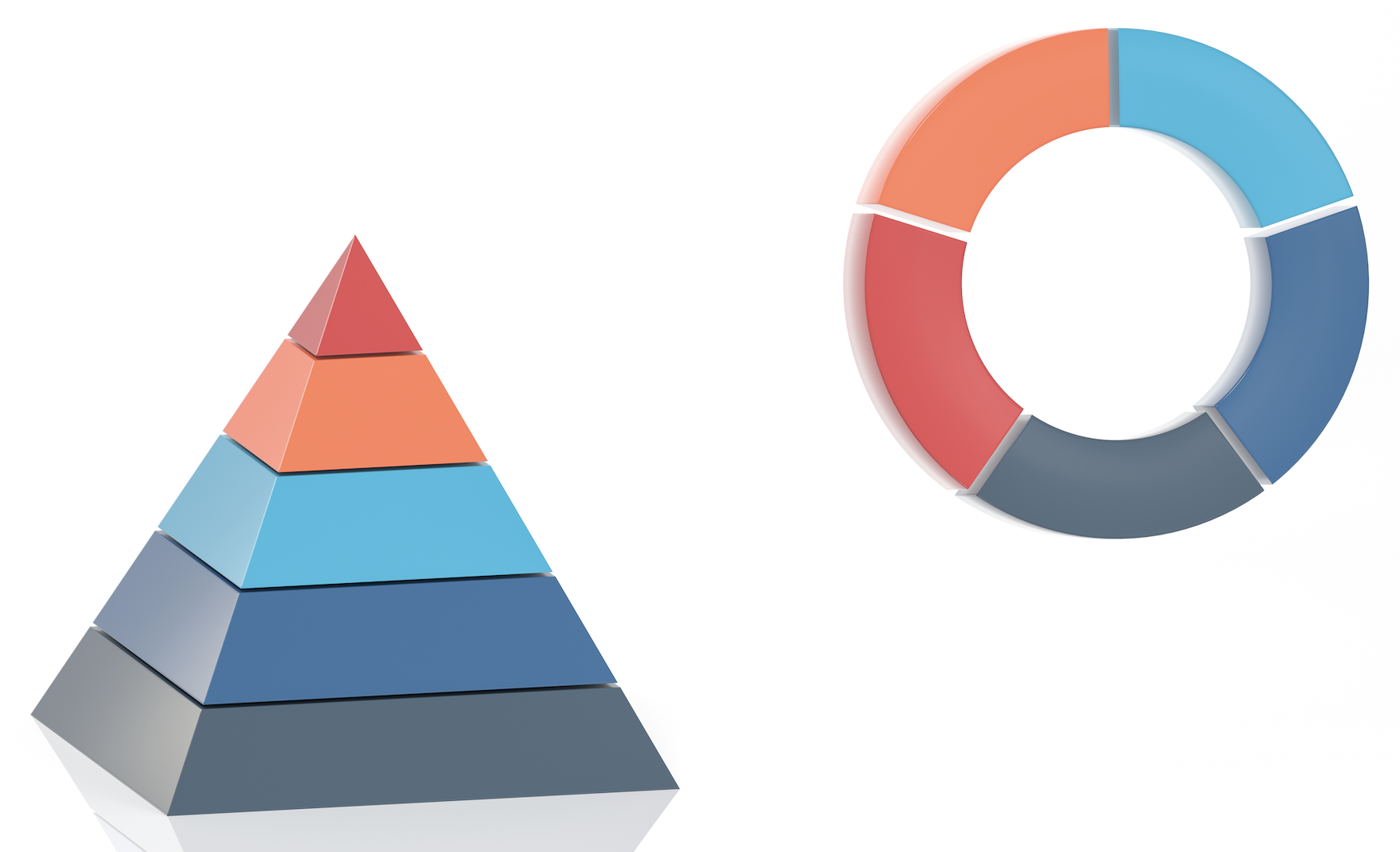
Aging and stability testing are critical components of the pharmaceutical and medical device manufacturing processes, designed to evaluate the long-term performance and quality of these products. These tests simulate the effects of various environmental factors, such as temperature and humidity, on the product’s physical, chemical, and microbiological properties over time.
By conducting these tests, manufacturers can determine the product’s shelf life, recommended storage conditions, and overall stability, ensuring that the final product maintains its intended quality, safety, and efficacy throughout its entire lifecycle. This is particularly important for ensuring the continued performance and reliability of medical devices and the therapeutic effectiveness and safety of pharmaceutical products.
Regulatory Requirements and Industry Standards
The pharmaceutical and medical device industries are subject to stringent regulatory requirements and guidelines when it comes to aging and stability testing. Regulatory bodies, such as the U.S. Food and Drug Administration (FDA) and the International Council for Harmonisation of Technical Requirements for Pharmaceuticals for Human Use (ICH), have established comprehensive guidelines and standards that manufacturers must adhere to.
These regulations outline the specific testing protocols, environmental conditions, and data analysis requirements that must be followed to demonstrate the stability and shelf life of pharmaceutical and medical device products. By complying with these standards, manufacturers can ensure that their products meet the necessary quality and safety thresholds, both during the initial product development and throughout the post-market lifecycle.
Aging and Stability Testing Methodologies
Pharmaceutical and medical device manufacturers employ a range of aging and stability testing methodologies to evaluate their products. These may include:
- Accelerated aging tests: These tests expose the product to elevated temperatures and humidity to simulate the effects of long-term storage and usage in a shorter timeframe.
- Real-time aging tests: These tests monitor the product’s performance under recommended storage conditions over an extended period, typically the expected shelf life of the product.
- Compatibility and interaction testing: These tests assess the compatibility of the product with its packaging materials, as well as any potential interactions between the product’s components or with other substances it may encounter during storage or use.
The data collected from these tests is then analyzed to determine the product’s stability profile, including its expiration date, recommended storage conditions, and any necessary packaging or formulation adjustments.
Data Analysis and Interpretation
Manufacturers carefully analyze the data collected from aging and stability tests to draw meaningful conclusions about the product’s performance and quality. This includes evaluating changes in the product’s physical, chemical, and microbiological properties over time, as well as any potential degradation or impurities that may arise.
By interpreting these test results, manufacturers can establish the product’s shelf life, define appropriate storage and handling conditions, and identify any necessary quality control measures to ensure the continued safety and efficacy of the product throughout its lifecycle. This information is then used to support regulatory submissions, product labeling, and post-market surveillance activities.
Importance of Aging and Stability Testing in Product Development and Lifecycle Management
Aging and stability testing are integral components of the pharmaceutical and medical device product development and lifecycle management processes. These tests provide critical insights that inform decision-making at every stage, from initial formulation and design to post-market monitoring and product improvements.
By understanding the long-term stability and performance characteristics of their products, manufacturers can make informed decisions about manufacturing processes, packaging, and distribution, ultimately ensuring the consistent quality and safety of their offerings. Additionally, the data generated from these tests can be used to support product labeling, regulatory compliance, and post-market surveillance efforts, contributing to the overall lifecycle management of the product.
In the highly regulated and quality-driven pharmaceutical and medical device industries, aging and stability testing are essential for maintaining the integrity, safety, and efficacy of these critical products, protecting both patient well-being and public health.
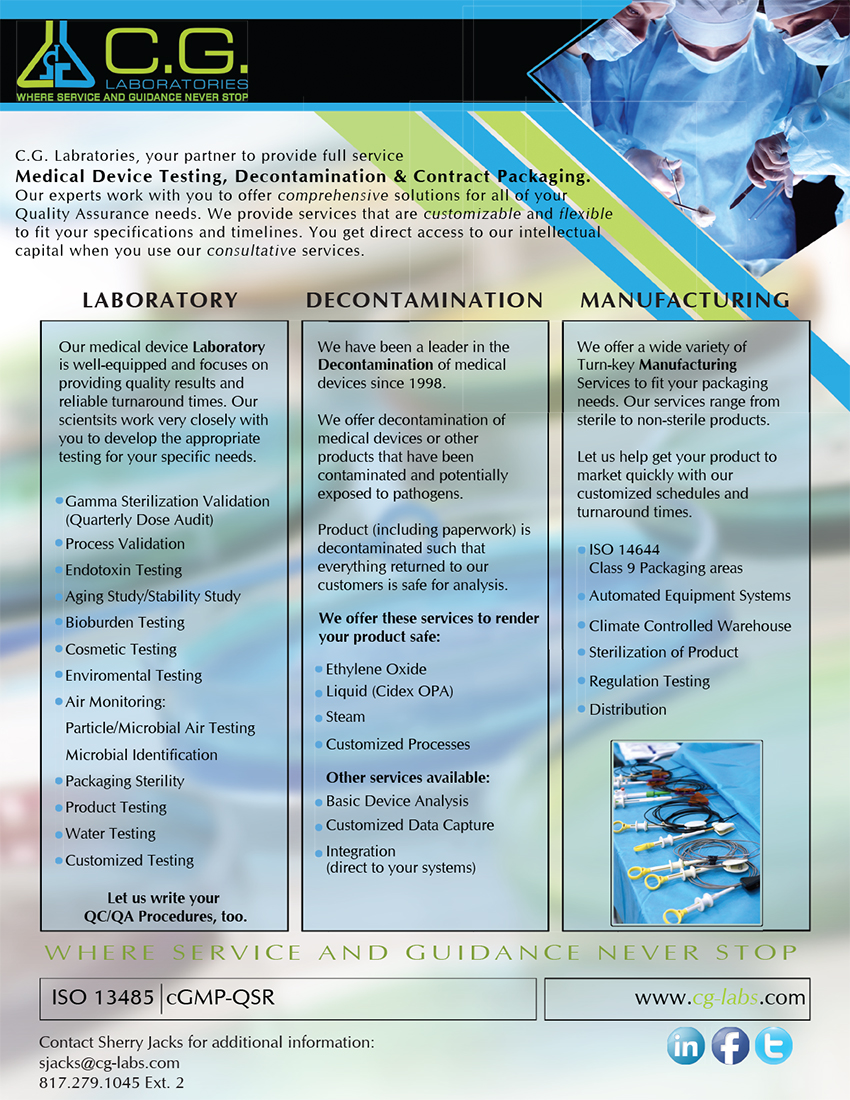